Curly Maple Table Top & Base
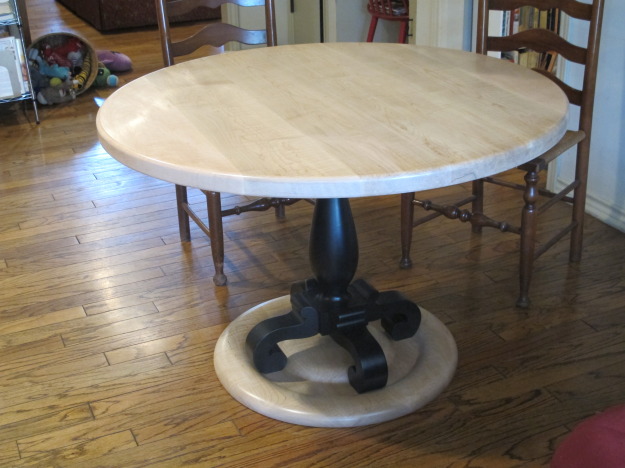
Clients brought a painted black table base to us to have a new table top made for it. The base had significant emotional and historical meaning to the wife as it had been in her family for generations as seen in this picture of her in 1949 standing next to her grandfather holding her cousin with the original mahogany pedestal end table in the background. The clients had adapted the table over the years to now function as a breakfast table for their spacious and inviting kitchen area.
After looking at wood samples, they chose a highly figured Curly Maple wood for the new table top. Since they were also wanting to increase the diameter of the table top, Mark worried about the “moment of tilt” factor with just the original base if someone used the edge of the table to hoist themselves out of their chair. Mark recommended that a base be attached to the bottom of the pedestal to increase the table’s stability.
Mark searched for the most highly figured maple and ended up ordering the wood out of a company in PA. It was indeed beautiful wood, but when Mark put a moisture meter to the wood, he was getting moisture readings of 12% which was just too high for him to trust how the glue joints would hold up once in the HVAC of the client’s home. He consulted with many wood drying experts and finally decided to build his own mini-kiln in the shop with a tarp, small dehumidifier, heat, and a fan to keep the air moving around the wood. This drying process ended up taking two months to finally reach an acceptable 8.5% moisture content and the clients very graciously accepted this delay in production.
The treasured pedestal now has new life as a very functional table where the owners will share many a meal and conversation with friends in their warm and hospitable home.
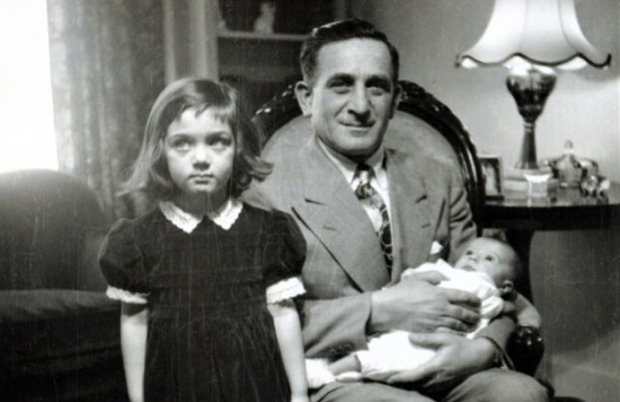
Photograph of our client in 1949 standing next to her grandfather holding her cousin with the original mahogany pedestal end table in the background.
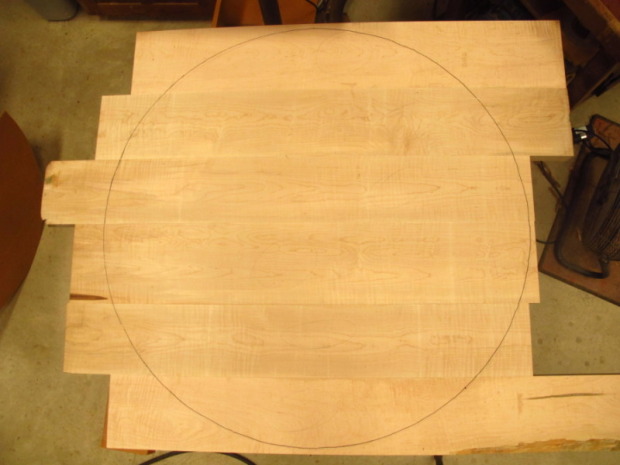
The drying process ended up taking two months to finally reach an acceptable 8.5% moisture content to assure reliable glue joints.